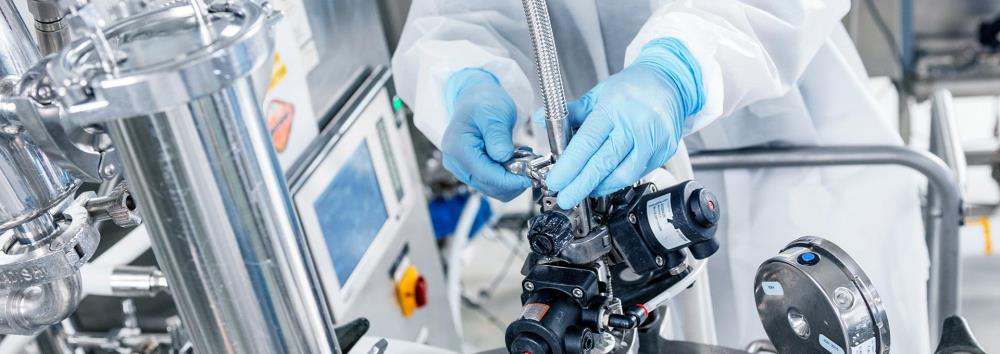
Visual Inspection Practices of Cleaned Equipment: Part I
Copyright PDA. Reprinted with permission.
Regulatory and compendial guidelines require that manufacturers confirm process equipment is visually clean following a cleaning operation. Recently, a STERIS survey showed that visual inspection practices for cleaned equipment differ among manufacturers. At the same time, the survey indicated that while practices and even terminology may differ, this can be accepted by regulators provided processes are well documented.
First, a word about terminology, many regulatory guidelines and industry technical documents use different terms to describe the step confirming process equipment is visually clean after cleaning. For the purposes of this article, the authors use the term “visual inspection.” Other common terms for this step are ”visual check” or ”visual examination.” Note that in this case, “visual inspection” does not refer to visibly checking finished product for particles.
For the survey, 39 responded, representing many European pharmaceutical and biopharmaceutical companies (27 companies in 34 different sites). The manufacturers who completed the survey were: 54% non-sterile (e.g., tablet, liquid, combined product), 13% sterile (e.g., biotechnology, liquid, and lyophilized product), 26% vaccine, 5% medical device, 2% other (e.g., early clinical production).
The European Annex 15 states that “A visual check for cleaning is an important part of the acceptance criteria for cleaning validation” (1). Visual inspection is a critical step to confirm the effectiveness of cleaning process equipment after cleaning. The acceptance criteria for visual inspection is visually clean. The visual inspection should include direct and indirect product contact surfaces, and requires the equipment surfaces to be visible. When this is not the case, dismantling the equipment to gain access, or using tools such as mirrors, light sources, or borescopes may be required (2, 3). Modern technology such as digital cameras capable of assessing the surface may also be explored for large-volume vessels, when a visual inspection is challenging.
Visually clean is the minimum standard expected. An additional acceptance criterion, such as the health-based limit, however, is enforced (1-5). Therefore, a validated analytical method with a sensitivity below the cleaning limit should be periodically coupled with a visual inspection. When applying only visual inspection to determine the cleanliness of equipment, the threshold at which the product is readily visible as a residue should be established (3, 6).
The visual inspection is always performed (to whatever degree possible) at the end of a complete cleaning cycle (7). The visual inspection is an active and qualitative observation of product contact surfaces to confirm the absence of residue and the next batch production can start (7). ICH Q7: Practice Guidance for Active Pharmaceutical Ingredients states that: “12.76 … Visual inspection can allow detection of gross contamination concentrated in small areas that could otherwise go undetected by sampling and/or analysis.”
Back to the survey, 54% of respondents are performing a visual inspection of the equipment surface when it is dry (Figure 1).
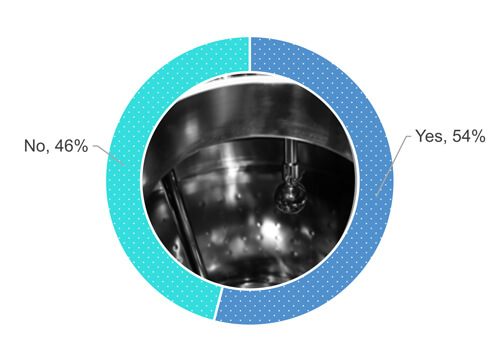
Figure 1 Does your company procedure require you to visually inspect the process equipment surface after a cleaning operation when the surface is dry?
Some technical industry documents suggest that visual inspection should be performed on a dried surface, when possible, to avoid false-negative results (8,9):
Active Pharmaceutical Ingredients Committee Guidance (10):
“After cleaning procedures are performed, equipment should be dried to allow the visual inspection.”
“The acceptance criteria for equipment cleaning should be based on visually clean in dry conditions and an analytical limit.”
PDA Technical Report No. 29: Points to Consider for Cleaning Validation (9): “Ordinarily surfaces that are visually examined should be dry, as this represents a worst-case condition for visual inspection.”
It is commonly known that for some residues, visually clean may only be achieved when the surface is wet, while this is no longer the case when the surface dries.
Equipment design and cleaning cycle parameters may conduct to dry the equipment surfaces, such as having the piping sloped toward the drain, being self-drainable, and the final rinse performed at high temperatures. In some cases, clean air blown into the equipment and the distribution system may help to achieve dryness on surfaces (9).
Despite these parameters listed above being met, however, droplets or moisture (“sweat”) on the surface could potentially be observed and may be acceptable if adequately justified.
As Figure 1 shows, 48% out of 54% who responded “yes,” when asked if they visually inspect equipment surfaces when entirely dry (Figure 2). 24% out of the 54% allow some partial wetness (e.g., isolated drops or sweat) of the surfaces during a visual inspection of the cleaned equipment (Figure 2). 19% out of the 54% accept numerous drops but no pooling of water. 9% out of the 54% have not defined the dryness requirements.
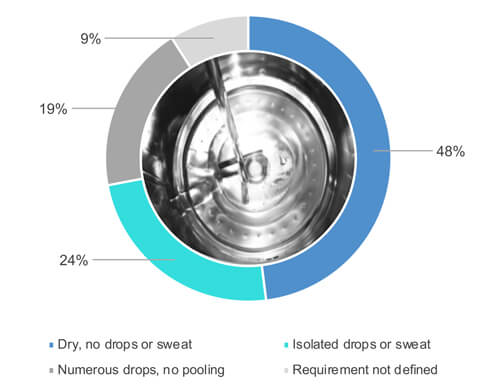
Figure 2 What is the dryness requirement for process equipment following the cleaning cycle is finished?
Different levels of dryness are acceptable if adequately justified and backed up by data demonstrating the absence of impact on the visual inspection post-cleaning and bioburden proliferation during clean storage, e.g., robust instruction and training using photos to avoid deviation. Finally, none of the 54% of the manufacturers that visually inspect their equipment when the surfaces are dry authorize for standing or pooling water on the equipment surfaces, as suggested in the U.S. FDA inspections guide (10): “…For example, equipment should be dried before storage, and under no circumstances should stagnant water be allowed to remain in equipment subsequent to cleaning operations.”
Considerable responsibility is given to an operator to decide whether equipment surfaces are visually clean. Therefore, the operators should be able to inspect all surfaces of the equipment visually. If not possible, adequate or advanced tools should be available to guarantee proper decision making (2, 3, 9, 11). A visual inspection of a large vessel through a sight glass is restrictive due to hidden surface. EMA suggests that the ability to visually inspect the equipment, such as distances observed in the field, should be taken into consideration in a Q&A document (3), recommending that “written instructions specifying all areas requiring visual inspection should be in place and records clearly confirm that all inspections are completed.” Finally, detailed procedures and training on visually clean criteria are mandatory to ensure correct decision making. The level of training and qualification to visually inspect should be commensurate by the risk of cross-contamination (3, 7, 9, 11).
When it comes to photos, 38% of the respondent surveyed have defined visually clean criteria by also adding photos and examples of clean status (Figure 3). 46% rely on the operator’s understanding of visually clean, coupled with a theoretical definition of visually clean in the procedure. Finally, 16% (3% and 13%) rely on the operator’s experience and training (using specific support or pictures) of a visually clean surface (Figure 3).
Figure 3 Does your company define and detail the meaning of “visually clean” criteria?
Operators performing visual inspection require specific training because what one can visually see varies with the distance, angle, lighting, the nature of the surface, the dryness level and the inspector’s visual acuity (3, 7, 9). EMA suggests that eyesight testing (or visual acuity) should be performed periodically, and the competency of the operator should be proven through a practical assessment (3). The ISPE Risk Mapp suggests that: “In situations where the method of detection is visual only, it is important to understand the visual acuity of the staff, and what level of residue is considered safe (7). If the safe level is below the visual acuity of the staff then the risk of failure not being detected may be considered high whereas if the safe level is well above (several orders of magnitude), the visual acuity of the staff the risk of failure not being detected may be considered low.”
The frequency of visual acuity test and visual acuity limit would depend on specific variable such as the:
- distance between the inspector and the inspected equipment surface (3, 7, 12)
- equipment configuration and surface nature (7,8)
- surrounding lighting conditions (3, 7, 9, 12)
- frequency of analytical testing (3, 7-9, 11,12)
- residues toxicity, cleaning limit versus visual detection limit (3,6,7)
- visual inspection only is performed to confirm the cleanliness of an equipment (7)
38% of the respondents do not require an operator’s certification or qualification (Figure 4). Yet 49% train their operators to visually clean on the field (in front of the equipment). Finally, 13 % qualify their operators.
Figure 4 Does your company have a certification or qualification program in place for visual inspection?
Some manufacturers have defined the visual residue limit, using coupons, an operator could detect (13, 14). Also, some of them mimicked the distance between the operator and the surfaces to be inspected on process equipment (15, 16). When the visual residue limit is lower than the cleaning limit visual inspection alone as an acceptance criterion may be enough (7).
Does a certification or qualification along with a training program ensure operators’ competency to inspect a surface visually? Following the precept of ICH Q9: Quality Risk Management (17), the answer would generally depend on the:
- number of historical visual inspection deviation due to operator training
- difficulty in inspecting the equipment (equipment configuration and background environment such as lighting, angle, etc.) (3, 7–9, 11, 12, 18, 19)
- type of visual inspection being used; qualitative or quantitative visual inspection (7,12, 13–16, 18,19)
- visual inspection is not supplemented with analytical testing (13–16,18)
- frequency of analytical testing performed with visual inspection
- analytical method sensibility against the cleaning limit, toxicity (based on the health-based exposure limit) of the residues (1–7, 9,11)
- presence of a double-check
Conclusion
The visual inspection concept and “visually clean” criteria seem to vary among European manufacturers based on their experience with the cleaning process execution and understanding of the regulatory requirements. The visually clean criteria, however, must be clearly defined in the procedures. Operators performing visual inspection require specific training, which can be based on their own experiences.
The variability in practices between manufacturers, as suggested by the survey results, may be acceptable when the risk is documented. Following the precepts of ICH Q9, the level of effort and formality should be commensurate with the patient’s risk.
In the Part II, a case study and suggested minimal requirement for visual inspection of cleaned surfaces will be presented.
European manufacturers interpret the criteria for “visually clean” in various ways, based on their experience executing the cleaning process and on their own interpretations of the regulatory requirements (1). Still, a formal visual inspection training and qualification program and instructions should be established to prevent the risk of contamination and to verify that equipment is cleaned based on a manufacturer’s set of controls (2).
Variability in practices between manufacturers is acceptable. Operators, however, must be periodically trained and qualified on when to visually inspect clean equipment and how to distinguish between product residue and surface imperfections that may impact the visually clean criteria. The case study below illustrates why this is important.
Case Study: Inspection Observation on Visual Inspection
Recently, U.S. FDA inspectors delivered an observation to an anonymous biopharmaceutical manufacturer regarding visually clean criteria. During a tour of the company’s shop floor, one of the inspectors checked out the upstream room where two fermenter vessels were located. The vessels are part of a closed system and are cleaned using a fully automated clean-in-place (CIP) system. The CIP cycle of one of the fermenters finished one hour before the inspector entered the upstream room. The inspector looked inside the vessel through the sight glass, observed a few condensation droplets and noticed the surfaces were not shiny. This did not convince the inspector that the vessel was “visually clean” (Figure 1).

Figure 1 Some chemical fingerprints (discoloration-trace) detected on the inner surface of the fermenter.
This led to the following observation: “Discoloration was observed in Fermenter (Equipment ID XXXX). This specific issue had not been evaluated by the firm. This fermenter is used for [product name] fermentation.” [Editor's Note: Quotes are from the resulting regulatory document.]
This observation raised a lot of questions and impacted several control strategies. Since it occurred after a cleaning cycle where a systematic (routine) visual inspection was carried out, it affected the cleaning control strategy and the maintenance program in place to ensure that the vessel surfaces were in an acceptable condition. These two programs were not aligned on how to inspect and manage vessels. What could be more practical than a daily visual inspection to confirm an acceptable surface state before confirming the visually clean status?
The biopharmaceutical company was able to justify the presence of droplets after the CIP process was completed as acceptable, mainly because the clean hold-time (CHT) was successfully validated in similar clean conditions. The inspector understood the situation (that the equipment was observed immediately after the CIP process) and accepted the justification.
Regarding the discoloration on the vessel wall, there was also an explanation. Various conditions may generate discoloration of the stainless steel when it is in contact with specific products, chemical agents or thermal effects. This is known as the surface internal weathering effect. The change in the surface may change the visual inspection condition, which may alter an inspector’s (or operator’s) decision on whether the surface is visually clean—even if the manufacturer has a high-quality training and qualification process.
The observation itself is clear: the “discoloration…had not been evaluated” while the equipment was being used on a routine basis to produce biological bulk. It did not, however, refer to a specific requirement.
How did the firm respond to this observation?
- The firm acknowledged that surface discoloration was detected during the FDA inspection and had not been evaluated before the inspection.
- An immediate action was implemented to investigate the discoloration, samples were taken for analysis, and the fermenter was not used.
The investigation demonstrated that decontaminating the vessels using caustic or other chemical agents at high temperatures (greater than 100 °C) stressed the vessel walls and could cause a chemical reaction to appear on stainless steel surfaces. Electropolishing only temporarily restores the surface of the vessels. Indeed, the decontamination and cleaning processes have since then generated discolorations on the internal surfaces of the fermenter.
There is a lesson to be learned from this FDA observation: The scope of the visual inspection by an inspector (e.g., operators or technicians) after a cleaning process should be well defined. The decontamination and the cleaning processes make a lasting impact on the structure of equipment over time. The processes in place for cleaning, decontamination and maintenance must be consistent, aligned and phased. Therefore, the cleaning and maintenance control strategy must be able to address the following challenges:
- How to evaluate and document the “visual imperfections” of the material that constitutes the equipment
- How to adequately define an acceptable dryness level prior to visual inspection
- How to train inspectors (operators, technicians and subject matter experts) to visually clean and to acceptable surface imperfections?
- How to define a surface imperfection that would lead to equipment disqualification
- How to determine if the role of visual inspection should include the control of surface imperfections?
How to Inspect for Visually Clean Status
Most inspectors (operators) throughout the industry have been inspecting and releasing manufacturing equipment based on experience (1,2). Yet, distinguishing product residue and surface imperfections could be difficult for operators.
To address that issue, operators should be trained on equipment constructed of the same materials and in the same situation that presents the target residue(s) they will be expected to visually detect. The training procedure and support to ensure reproducible visual inspection should contain, at least, the following sections:
1. Definition of visually clean criteria
Visually clean, defined as “the absence of visible residue on a surface,” should be properly defined as an acceptance criterion in the procedure.
In addition to descriptions, pictures (Figure 2) of visually clean surfaces in a procedure or training course are the best option. The visual inspection could detect much more than product residue.
Recent studies demonstrated that training the inspector to differentiate between residue on the surface and noncritical surface imperfection or discoloration is important to visually inspecting clean surfaces (2, 3). In some cases, operators could be made aware of the level of discoloration or imperfection that is acceptable on the surfaces, as some consider this surface control as part of the maintenance or engineering program.
The level of acceptable dryness of equipment or the drainability category and conditions could be made part of the definition or could be included in a cleaning risk evaluation.
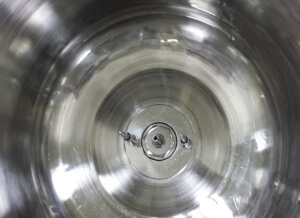
Figure 2 Visually clean surfaces after a cleaning process.
2. Scope of the visual inspection
Which surfaces must be visually inspected? All equipment surfaces that directly or indirectly contact the product, bulk or intermediate material should be visually inspected. As not all surfaces of a piece of equipment may be visible for visual inspection, the scope could be tailored to the type of equipment. How and what to visually inspect on the surface should be discussed.
3. Surrounding conditions to visually inspect a clean surface
The conditions surrounding the equipment to be visually inspected impacts the ability to properly detect residue, making that environment an important element. The amount of detectable residue (visible reside limit) is product-dependent and needs to be defined on a case-by-case basis or by the grouping approach (2–6).
To confirm the impact of the surrounding conditions on a visual inspection, the following factors should be analyzed:
- Viewing distance: The distance between the surface and the operator. This viewing distance may not be easy to simulate in a laboratory; however, common sense dictates that the greater the distance, the harder the visual inspection may be. The inspector’s visual acuity at a specific distance also plays a role.
- Light levels (approx. from 400 to 1500 Lux in normal cleanrooms): Some coupon studies have indicated that light levels between 200 and 1400 Lux may not alter an inspector’s visual inspection; still, this should be demonstrated via actual situations.
- Viewing angle: The viewing angle between the inspector’s eyes and the surfaces to be visually inspected should also be considered and integrated into the process of visual inspection. Depending on the angles and the light levels, an inspector may see some reflections that would make it difficult to confirm visually clean.
- Secondary light: The use of a flashlight is not recommended when the cleaning validation runs were not inspected with a flashlight. Conditions of inspection must be similar between validation runs and routine cleaning and maintenance.
Understanding the surrounding factors that may alter visual inspection is key to preventing inadequate decisions.
4. Timing of performing visual inspection
A visual inspection should be performed after a completed cleaning operation. At the same time, this is often not part of the documentation and can result in questions about conducting the visual inspection conducted in the event a cleaning cycle is aborted. The procedure should specify how long after the end of the cleaning cycle a visual inspection should be performed. This timing should be determined to ensure the operator is safe when opening a vessel (e.g., the rising step is generally performed at high temperatures). This timing impacts the water or solvent draining process and could prematurely invalidate the inspection.
5. Methodology to visually inspect
A structured methodology to visually inspect clean equipment should be established. For example, a manufacturer could develop a checklist that identifies the various parts of the equipment to be visually inspected in a coherent visual path. In addition to following the method for general visual inspection, some manufacturers have developed checklists identifying specific parts or known worst-case locations that should be visually inspected.
6. Identifying the visible targeted residue(s)
Operators should be introduced to all the elements they may examine during the visual inspection. These elements could include the product residue, surface imperfections, surface damages, residual water and particles, among others.
The operator will inspect the visible surfaces with all their imperfections. They will also be able to detect many other elements or anomalies, starting with defects related to the material, its aging, traces of residual water, particles, and product residues (Figure 3). Therefore, the visual inspection target and acceptance criteria must be clearly defined.
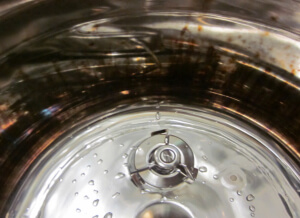
Figure 3 Elements operators should detect on a direct or indirect product contact surface.
The level of formality in developing these six sections depends on the company’s cleaning risk assessment and control strategies.
Conclusion
Visual inspection is the method of choice to confirm visually clean status. Most inspectors (operators) throughout the industry have been inspecting and releasing manufacturing equipment based on experience (1,3). It could be difficult, however, for operators to distinguish product residue and surface imperfections without proper training and qualification. Consequently, properly training operators and making sure all materials of construction and in similar situation are offered to visually detect the target residue(s) and surfaces imperfection that could impact the visually clean status makes sense. A formal visual inspection training and qualification program as well as instructions should be established. This program should be based on the set of controls the manufacturer uses to verify equipment is clean. Therefore, visual inspection as defined and qualified could be a preliminary control method for a cleaning risk management strategy.
Both authors were involved in drafting the manuscript and approved the final version. The development of this article was sponsored by GlaxoSmithKline Biologicals SA and STERIS. The authors declare the following interest: Walid El Azab is an employee of STERIS, Stephane Cousin is an employee of the GSK group of companies.
Part 1 References
- European Commission, Good Manufacturing Practice Medicinal Products for Human and Veterinary Use: Annex 15, qualification and validation, 2015.
- Canada Health Products and Food Branch Inspectorate. Guidance Document. Cleaning validation guidelines: Drug and health products. Health Canada: Ottawa, Canada; 2002 Spring.
- European Medicines Agency, Questions and answers on implementation of risk-based prevention of cross-contamination in production and ‘Guideline on setting health-based exposure limits for use in risk identification in the manufacture of different medicinal products in shared facilities’ (EMA/CHMP/CVMP/SWP/169430/2012), EMA/CHMP/CVMP/SWP/246844/2018, (April 2018)
- European GMP part IV Guidelines on Good Manufacturing Practice specific to Advanced Therapy Medicinal Products
- Pharmaceutical Inspection Convention and Pharmaceutical Inspection Co-operation Scheme. Guide to Good Manufacturing Practice for Medicinal Products: Annex 15, 2015.
- Walsh A. et al., “Justification & Qualification Of Visual Inspection For Cleaning Validation In A Low-Risk, Multiproduct Facility.” Pharmaceutical Online (Aug. 3, 2018) accessed January 2020 https://www.pharmaceuticalonline.com/doc/justification-qualification-of-visual-inspection-for-cleaning-validation-in-a-low-risk-multiproduct-facility-0001
- ISPE, ISPE Risk-Based Manufacture of Pharmaceutical Products, second edition, Volume 7
- Active Pharmaceutical Ingredients Committee, guidance on aspects of cleaning validation in active pharmaceutical ingredient plants (2016)
- Parenteral Drug Association, Technical Report 29, Points to Consider for Cleaning Validation (2012)
- GUIDE TO INSPECTIONS VALIDATION OF CLEANING PROCESSES, accessed on September 2019: https://www.fda.gov/inspections-compliance-enforcement-and-criminal-investigations/inspection-guides/validation-cleaning-processes-793
- Parenteral Drug Association, Technical Report 49, Points to Consider for Biotechnology Cleaning Validation (2010)
- ASTM: E306-18, Standard guide for Science-Based and Risk-Based Cleaning Process Development and Validation, October 2018 version 1.
- Forsyth, R.J., et al. “Visible-Residue Limit for Cleaning Validation and its Potential Application in a Pharmaceutical Research Facility.” Pharmaceutical Technology 28 (Oct. 1, 2004) 68–72.
- “Application of Visible-Residue Limit for Cleaning Validation.” Pharmaceutical Technology 28 (Oct. 2, 2005) 10 http://www.pharmtech.com/application-visible-residue-limit-cleaning-valiation?id=&pageID=1&sk=&date= (accessed September 2019)
- “Determination of Surface Visible Residue Limits on Pharmaceutical Plant Equipment.” Pharmaceutical Technology 37 (Feb. 2, 2013)
- Desai, P., and Walsh, A. “Validation of Visual Inspection As An Analytical Method For Cleaning Validation.” Pharmaceutical Online (Sept. 11, 2017) https://www.pharmaceuticalonline.com/doc/validation-of-visual-inspection-as-an-analytical-method-for-cleaning-validation-0001 (accessed September 2019)
- International Conference on Harmonization of Technical Requirements for Registration of Pharmaceuticals for human use, Quality Risk Management Q9, (2005)
- Walsh, A., et al., “Justification & Qualification Of Visual Inspection For Cleaning Validation In A Low-Risk, Multiproduct Facility.” Pharmaceutical Online (Aug. 3, 2018) https://www.pharmaceuticalonline.com/doc/justification-qualification-of-visual-inspection-for-cleaning-validation-in-a-low-risk-multiproduct-facility-0001 (accessed January 2020)
- Forsyth, R.J., and Hartman, J., “A Risk-based Approach to Cleaning Validation using Visible Residue Limits.” Pharmaceutical Engineering 28 (2008) 8–22.
Part 2 References
- El Azab W. and Cousin S., “Visual Inspection Practices of Cleaned Equipment: Part I,” accessed April 2020: https://www.pda.org/pda-letter-portal/home/full-article/visual-inspection-practices-of-cleaned-equipment-part-i
- Walsh, A., et al., “Justification & Qualification of Visual Inspection for Cleaning Validation in a Low-Risk, Multiproduct Facility.” Pharmaceutical Online (Aug. 3, 2018) https://www.pharmaceuticalonline.com/doc/justification-qualification-of-visual-inspection-for-cleaning-validation-in-a-low-risk-multiproduct-facility-0001
- Desai, P. and Walsh, A. “Validation of Visual Inspection as an Analytical Method for Cleaning Validation.” Pharmaceutical Online (Sept. 11, 2017) https://www.pharmaceuticalonline.com/doc/validation-of-visual-inspection-as-an-analytical-method-for-cleaning-validation-0001
- Forsyth, R.J., et al. “Visible-Residue Limit for Cleaning Validation and its Potential Application in a Pharmaceutical Research Facility.” Pharmaceutical Technology 28 (Oct. 2004): 58–72 https://pdfs.semanticscholar.org/ea64/d01db84d3b8a5a62f1c824abf8484af363dd.pdf
- “Application of Visible-Residue Limit for Cleaning Validation.” Pharmaceutical Technology 29 (Oct. 2, 2005) http://www.pharmtech.com/application-visible-residue-limit-cleaning-validation?id=&pageID=1&sk=&date=
- “Determination of Surface Visible Residue Limits on Pharmaceutical Plant Equipment,” Pharmaceutical Technology (Feb. 2, 2013) 37 http://www.pharmtech.com/determination-surface-visible-residue-limits-pharmaceutical-plant-equipment?id=&pageID=1&sk=&date=